Iron Smelt - Wareham, ON - June 11, 2011
Date:June 11, 2011
Location:Wareham, ON
See also: Darrell Markewitz's ironsmelting site
Team: Neil Peterson, Richard Schwietzer, Sam Falzone, Darrell Markewitz
Premise: Practice for CanIron8 presentation.
Furnace Design
Type | EconoNorse in a can (enclosed fire brick), tap arch |
Extraction | dismantled |
Diameter | 25 cm |
Height | 65 cm |
Volume | 31890.625 cm3 |
Tuyure Type | ceramic tube |
Tuyere height from base | 20 cm |
Tuyere penetration into furnace | 5 cm |
Tuyere angle | 22 deg |
Base design | natural set base cm |
Burn Details
Bellow Type | blower |
Avg Air rate | 800-900 litres per minute |
Total Charcoal Mass | 48 Kg |
Avg Burn rate | min per 2 Kg |
Ore Type | Bratton's Run |
Total Mass of Ore | 24-29 Kg |
Burn Duration | 4:45 Hours |
Results
Mass of Bloom | 2.65 Kg |
Bloom Type | Soft forgable iron |
Yield | 10% |
Notes | |
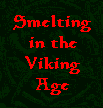 |
Reports of all of our iron smelting efforts along with more articles and information are available on the "Iron Smelting in the Viking Age" CD from the Wareham Forge. Copies of the CD can be purchased here. |
Discussion:
Conclusions:
The bloom produced was compacted considerably farther than our average (important in terms of yield comparisons). At time of extraction, the mass was considerably more spongy than for past smelts. Due to good hammer work by two visiting professional farriers, the bloom was compacted down to roughly the size of a pound of butter, then cleanly sliced into two rectangular slabs. On spark testing, the interior metal was found to be almost completely carbon free. This agrees with the striker's impression that this was soft forgeable iron.
The furnace itself was a well proven design, and although the working team was a bit lacking in self directed experience, the method followed was one developed through considerable past (successful) experience. Taken together, this certainly suggests the low yield was the result of the quality of the untested ore used for the smelt.
Photos:
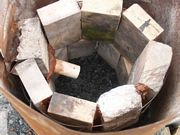 |
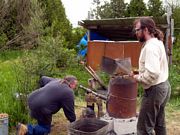 |
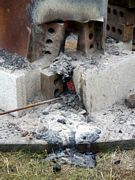 |
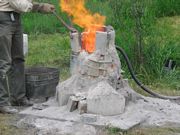 |
Early construction |
Mid Smelt |
Slag Tap |
Breaking down furnace |
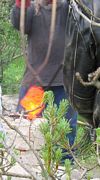 |
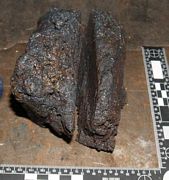 |
| |
Extracting the bloom |
finished bloom |
Raw Data:
CLOCK |
ELAPSED |
EVENT |
AIR |
CHARCOAL |
|
|
ORE |
|
|
|
|
|
|
|
UNIT |
COUNT |
TOTAL |
UNIT |
|
COUNT |
TOTAL |
|
|
|
LpM * |
bucket |
|
kg |
scoop |
added |
|
kg |
|
|
|
|
|
|
1.8 * |
|
|
|
0.35 * |
|
|
|
|
|
|
|
|
|
|
|
(8:30) |
|
team arrives on site |
|
|
|
|
|
|
|
|
(9:00) |
|
start furnace build |
|
|
|
|
|
|
|
|
(10:40) |
1:40 |
start pre-heat |
|
|
|
|
|
|
|
|
(11:00) |
:40 |
first charcoal addition |
|
|
|
|
|
|
|
|
|
|
|
|
|
|
|
|
|
|
|
|
|
re-set event clock |
|
|
|
|
|
|
|
|
12:00 |
|
ungraded charcoal to fill |
400 |
3 E |
3 |
5.55 |
|
|
|
|
12:40 |
:40 |
ungraded charcoal |
800 |
1 |
4 |
7.40 |
|
|
|
|
12:48 |
:08 |
graded charcoal |
|
1 |
5 |
9.25 |
|
|
|
|
12:59 |
|
added top collar |
|
|
|
|
|
|
|
|
13:02 |
:14 |
double charcoal addition (fill collar) |
|
2 |
7 |
12.95 |
|
|
|
|
|
|
ore additions started |
|
|
|
|
|
|
|
|
13:12 |
:10 |
charcoal & ore |
|
1 |
8 |
14.80 |
1 |
0.21 |
1 |
0.21 |
13:20 |
:08 |
charcoal & ore |
|
1 |
9 |
16.65 |
2 |
0.7 |
3 |
0.91 |
13:30 |
:10 |
charcoal & ore |
|
1 |
10 |
18.50 |
3 |
1.05 |
6 |
1.96 |
13:40 |
0:10 |
charcoal & ore |
|
1 |
11 |
20.35 |
3 |
1.05 |
9 |
3.01 |
13:52 |
0:12 |
charcoal & ore |
|
1 |
12 |
22.20 |
3 |
1.05 |
12 |
4.06 |
14:03 |
0:11 |
charcoal & ore |
|
1 |
13 |
24.05 |
4 |
1.4 |
16 |
5.46 |
14:15 |
0:12 |
charcoal & ore |
|
1 |
14 |
25.90 |
4 |
1.4 |
20 |
6.86 |
14:26 |
0:11 |
charcoal & ore |
|
1 |
15 |
27.75 |
5 |
1.75 |
25 |
8.61 |
14:28 |
|
adjust air |
900 |
|
|
|
|
|
|
|
14:35 |
:09 |
charcoal & ore |
|
1 |
16 |
29.60 |
6 |
2.1 |
31 |
10.71 |
14:46 |
0:11 |
charcoal & ore |
|
1 |
17 |
31.45 |
6 |
2.1 |
37 |
12.81 |
14:56 |
0:10 |
charcoal & ore |
|
1 |
18 |
33.30 |
6 |
2.1 |
43 |
14.91 |
15:03 |
0:07 |
charcoal & ore |
|
1 |
19 |
35.15 |
5 |
1.75 |
48 |
16.66 |
15:08 |
0:05 |
charcoal & ore |
|
1 |
20 |
37.00 |
5 |
1.75 |
53 |
18.41 |
15:14 |
0:06 |
charcoal & ore |
|
1 |
21 |
38.85 |
5 |
1.75 |
58 |
20.16 |
15:24 |
0:10 |
charcoal & ore |
|
1 |
22 |
40.70 |
6 |
2.1 |
64 |
22.26 |
15:35 |
|
slag tap |
|
|
|
|
|
|
|
|
15:38 |
0:14 |
charcoal & ore |
|
1 |
23 |
42.55 |
7 |
2.45 |
71 |
24.71 |
15:49 |
0:11 |
charcoal & ore |
|
1 |
24 |
44.40 |
6 |
2.1 |
77 |
26.81 |
15:55 |
0:06 |
charcoal & ore |
|
1 |
25 |
46.25 |
6.5 |
2.275 |
83.5 |
29.09 |
|
|
start burn down phase |
|
|
|
|
|
|
|
|
16:20 |
:25 |
last cover layer of charcoal |
|
1 |
26 |
48.10 |
|
|
|
|
16:41 |
0:21 |
extraction begins |
700 |
|
|
|
|
|
|
|
|
|
remove top layer of bricks |
|
|
|
|
|
|
|
|
|
|
|
|
|
|
|
|
|
|
|
|
|
|
|
|
|
|
|
|
|
|
|
AIR |
all approximate (guide marks only) |
|
|
|
|
|
|
|
|
|
CHARCOAL |
based on past average weight |
|
|
|
|
|
|
|
|
|
ORE |
based on average scoop weight |
|
|
|
|
|
|
|
|
|
|
|
|
|
|
|
|
|
|
|
|
TOTALS |
Charocal |
48 kg |
|
|
|
|
|
|
|
|
|
Ore - as scoops / bucket weight |
29 kg |
24 kg |
|
|
|
|
|
|
|
|
Time |
4:45 + |
|
|
|
|
|
|
|
|
|
Bloom |
2.65 kg |
|
|
|
|
|
|
|
|
|
Yield (estimate only) |
9% |
11% |
|
|
|
|
|
|
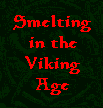 |
Reports of all of our iron smelting efforts along with more articles and information are available on the "Iron Smelting in the Viking Age" CD from the Wareham Forge. Copies of the CD can be purchased here. |