Two Icelandic Museums
This is a new museum (opened this year) housing Íslendingur, a knarr built by folks here in Iceland and sailed over to L'anse Aux Meadows in 2000. The museum is a little sparse for content but that isn't surprising with the money situation in Iceland. -- For those who don't know the banking crisis hit this tiny country very hard, with the three biggest banks going belly up, and the British and Dutch governments holding the country hostage to get repaid for deposits by their people. -- The museum was completed and opened which is a big credit to the people who worked on bringing it about.
The museum itself is Well laid out with the largest hall housing the boat which is displayed to provide wonderful visibility into, and under, the boat. There are view areas on the second floor allowing visitors to look down on the main deck, and on the main floors to allow visitors to walk underneath it. There is significant content about the creation of the ship and its voyage which is wonderful to see.
The remaining rooms have reasonable content, the layout gives you time and space to examine the artefacts, a very nice mural and room to expand the collection as time and money allow. Plus - they allowed pictures and the lighting wasn't awful! This is an important thing in a museum in my opinion, made even better by the listing of artefact numbers with the text about the item allowing easy followup with the curatorial staff. The text had a good balance of overall context and some information about the particular artefact. It didn't go into all of the detail that I might want to see but then again, I am not the average visitor. The gift store had a reasonable collection of books, but the other content was a bit sparse. Overall, it's well worth the time and money to visit, likely even more so as the years pass if they continue to build the content.
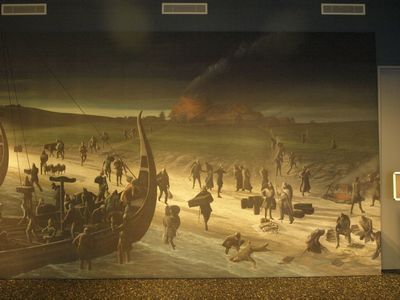
Part of the mural showing the raid on Lindisfarne.

Three of the arrowheads in the exhibit along with their associated text.
Clearly having too much time on his hands, Thorgrimr carved a small norse figure completing it just before our last get together. Needless to say the timing of this and our trip was too much fun to pass up - so we decided to drag Snorri along with us.
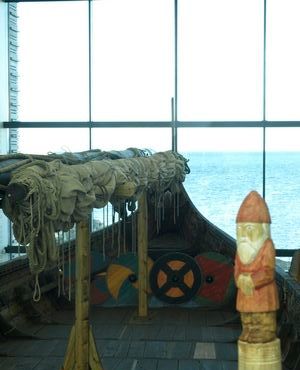
Here we see Snorri posing on the top deck of the Islandingur. Worth noting as a future expansion is that the back end of the boat has four nice boxes in it. All of them were closed - a nice addition would be to open one and show some of what would be stored in it. As a second point, surely ONE of them could be carved to allow a nice game of tafl while sailing? I think it might also be nice to put out an oar or two to allow people to see them in relation to the size of the boat and benches.
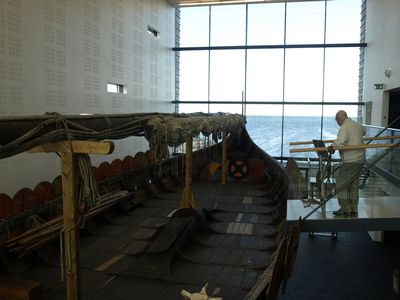
Part of the top viewing area allowing you to step quite close to the top of the boat and see each part of it.
The second museum was at Eiriksstaðir.
This museum is the likely first home of Eirik the Red's married life. It was occupied for only 10-20 years before he had to move on "due to some killings". The museum itself has a small staff shack, a set of washrooms, a half dozen full sized poster boards with the site history in four languages (Icelandic, English, German, and one of the Scandinavian languages). Just slightly uphill from the signs is the actual remains covered over again but with the wall outline shown as at L'anse Aux Meadows. A few yards off to one side is the reconstructed house where you find the two re-enactors.
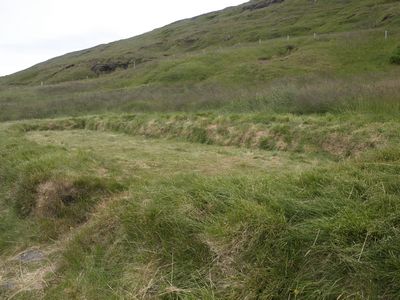
These are the re-buried remains of the original longhouse. Surprisingly small actually (4x12 m).
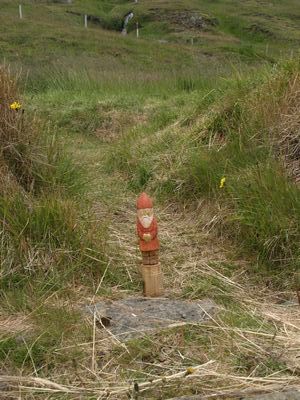
Here we see Snorri about to enter the archaeological remains of the original house.

The loom in the reconstructed house. I'll leave it to Karen to go into details about the differences between this "Icelandic" style loom and the scandinavian looms. The staff did mention that they don't work on the loom anymore as they had a lot of difficulty with it - wonder why....
They also mentioned that the fire keeps things dry enough inside that they are getting some heavy checking on the wood pillars. They often boil water (over the propane fire) to help increase the humidity.
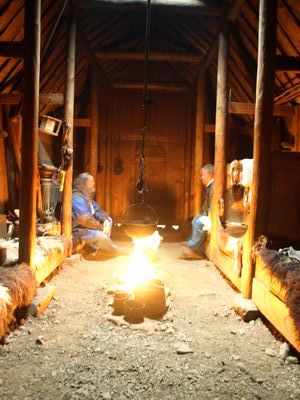
Karen grabbed this wonderful shot of my enjoying a story from the male staff member - funny we talked for a long time about a range of topics, I left each of them with a DARC card but none of us thought to introduce ourselves by name (or ask the other's name) - the things that don't occur to you until later... We will have to follow up by email with them later. In any case their presentation is entirely in third person story telling. They talk through the story of Eirik and Leif, birth, exile, new lands, all of it. There are only a very few staff members working now (a shame). The hall is fairly nice, and like the houses at L'anse Aux Meadows it cuts out the outside wind noise perfectly. It is, however, very heavily equipped. Multiple spears, a sword, multiple axes, many shields, sheepskins everywhere, bric a brac tucked in every corner, lots of clothes on the walls.
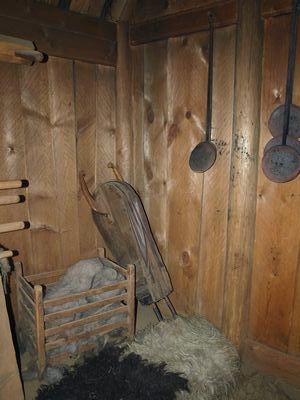
A bellows (not right for viking age unless they know something we don't) and an example of the equipment load - that is 4 frypans on the wall - riches!
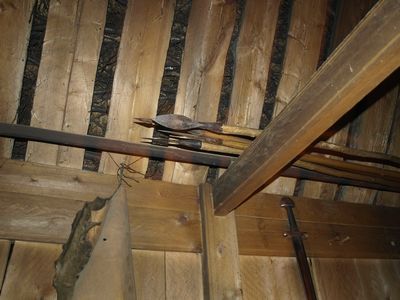
Some of the many weapons around the house.
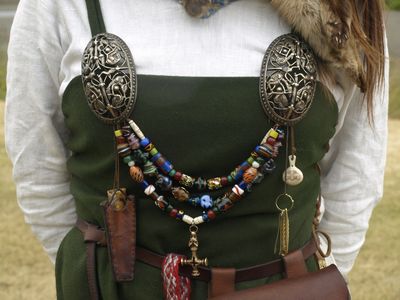
A closeup of the jewelry of the female interpreter (get the NAMES next time!). Being interested in beads, this was especially of interest to me. The middle strand she called out as a gift from a bead maker (extremely modern styles), the other two strands have a mix of the good and the bad. I'm not sure about the broaches, lovely work but they are cut-outs without a solid backing. Like a two piece broach without the underlying piece. Must look into this to see if any finds match that.
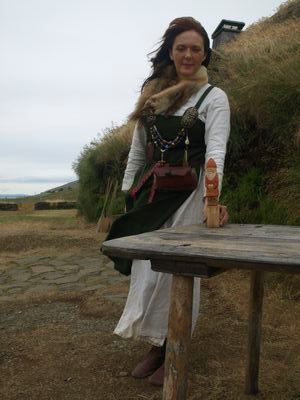
And just for fun the nice lady posed with Snorri allowing the costume types a look at her outfit. (nice fox as a scarf)
Overall, most definitely worth the time and money to visit. The folks there are quite knowledgeable about the history involved but not as much about the artefacts and they don't seem to be as active in the research. This is more of an acting arrangement.
Labels: Iceland, museums - teaching, photographs, travelogues