(Duplicate of post seen on 'Hammered Out Bits' )At the SCA event Trillium Wars over June 28-29, the 'Aristotle Furnace' was demonstrated by members of DARC.
The furnace design is the work of
Skip Williams, who researched the concept and had built a number of working prototypes to establish a method. I was taught the basics of its construction and operation at Smeltfest 08 back in March. In earlier posts there is a fuller description of the design and workings of this small furnace. It functions by melting scrap iron into a fresh 'puck' of mid to high carbon steel over a relatively short operating cycle.
The two images here are the only ones captured from the recent demonstration. Both images are by
Karen Peterson (of course I was engrossed in actually running the furnace.) My primary assistant for the entire process was
V. Meghan Roberts, who both helped with the messy work of building the furnace and breaking charcoal, but also proved to be a good bellows operator.
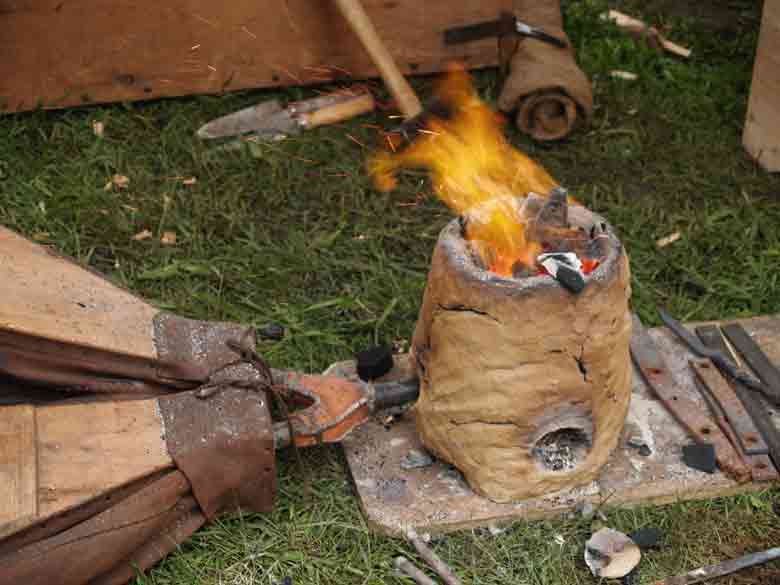
The first is a close up of the furnace itself in action. The body is made up of a mix of horse manure and powdered clay. I had the manure from my farm neighbour, and tried to gather older and drier material. About a half of a standard five gallon pail was first shredded by hand. (Fresh manure does not work up as well, being too moist to easily mix with the clay). To this was added about an equal volume of dry powdered ball clay (from our local pottery supply). Water was then slowly included, to create a mix roughly the consistency of bread dough. Each double hand full was worked to an even texture before it was applied to the furnace. Roughly a half bag of clay was required , a rough cost of about $10 (we had some unused cobb material left over).
The furnace was roughly 15 cm on the internal diameter, standing about 30 cm tall. (This was maybe a bit on the short side.) The base was a slab about 3 - 4 cm thick, the walls roughly the same. Initially there was a air hole cut into the side to fit the bellows tube. This was located about 5 cm up from the floor of the interior, and about 1 cm in diameter into the furnace. The outer side of this hole was roughly conical, to hold the 2 cm diameter bellows tube.
The furnace was constructed on the Saturday, then left overnight to allow the clay to stabilize and partially dry. (We had originally intended to fire on Saturday as well, but there was a lot of activity in the small work space, so we waited to reduce the confusion.)
At the start of the pre-heat phase on Sunday, it quickly became apparent that the single air port would only allow for combustion with the use of forced air from the bellows. As it is always important to provide a gentle heating until all the water is baked out of the clay structure, a second hole was cut into the base. This hole had tapered sides, about 5 cm in diameter on the inside surface. Taking a lesson from Jake Keen, there were two angled holes made to hold a pair of twig sticks. This allowed for manipulation of the plug later when it was hot. The shape caused the plug to be christened 'the pig nose'. The larger air intake allowed the wood splints of the pre-heat to burn correctly. This gentle heating would continue for about an hour and a half. Pre-heat was judged to be complete when there was no longer any white steam visible off the furnace's sides.
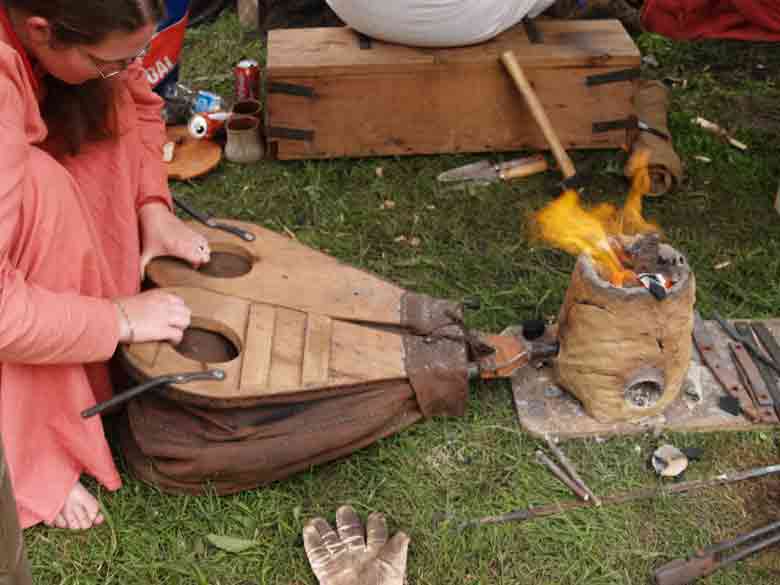
This shows the furnace and bellows combination, along with one of our many volunteer bellows operators. The bellows used is a Viking Age blacksmith's bellows, based closely on the two artifact sources (see earlier posts for a long discussion of this equipment). In total we ran the furnace through three cycles, with quite differing results from each. The primary reason for this inconsistency was the variation in air volumes created by the efforts of the various operators. Almost all of them had no experience with hand bellows, much less this specific Norse type. Not too surprisingly, those who had previous experience with the bellows type produced the most suitable air deliveries for the process at hand.
For the first cycle, the metal used was a short length (about 25 cm) of standard 1/2 inch round mild steel rod. The air delivery was by far the most suitable and consistent, as I undertook the bellows operation for this cycle. (I certainly was the only one who had ever seen the furnace in operation, plus had considerably more experience working hand powered bellows.) Mehgan also assisted on the bellows, but had paid close attention and pretty much duplicated my method and rates. The fuel was also smaller particles, as most of it had been gathered from what remained of the forging operation from earlier in the day. Most of the pieces were still ignited, lightly ash coated, and roughly 'walnut' sized. The end product of this cycle was the desired lump of higher carbon metal 'bloom', in this case with a short stub of the parent rod (about 3 cm worth) still attached.
Some problems with equipment placement caused a mad scramble getting this piece from the furnace to the anvil, so by the time the hammer was striking the metal had dropped to the low oranges. Even still the material proved to be forgable metal, at a guess a mid carbon steel (no grinder was available for spark testing).
For the second cycle, the metal used was a piece about 30 cm long of recycled wagon part, flat bar about 1/4 x 1 inch stock. The material had earlier been tested an appeared to be a lower carbon steel (not actual wrought iron) and was heavily surface pitted. The bellows operation for this sequence was far less consistent, with a lower air volume on average and thus both lower temperatures and longer consumption rate of fuel. This created both a slower conversion of the bar and also suggested more possible soak time to absorb carbon from the interior. In actual fact the end result proved to be a high carbon cast iron. The puck of material produced was not forgable, fragmenting under the hammer.
On the last cycle, the metal used was a piece of 3/8 square mild steel bar, again about 30 cm long, recovered from a damaged fire tool. A number of people took turns on the bellows, most significantly Sam, who had his blacksmithing experience from his Ango-Saxon forge to guide him. The air rates fluctuated most widely over this cycle. This again could be seen in the results. The metal fragmented under the hammer, with the bottom half splitting off clearly as brittle cast iron. The upper portion of the puck appeared to be useable metal, but was certainly tougher to shape that the metal from cycle one. On a guess this material should test out to a higher carbon tool steel.
Although the furnace did come through its repeated uses in reasonably good shape, it did not survive being dropped out of the truck while being unloaded the next day.
The method of manufacturing the furnace was well demonstrated, and the horse manure / clay mix seems idea for the construction. The general principle of this small steel furnace was again proven. It remains clear that bellows operation is the largest variable, with experienced operators being critical to the function of the furnace. The great advantages of this furnace, ease of construction and speed of a single use cycle was again demonstrated. More work needs to be done to fine tool the correct sequence, which repeated uses to accumulate experience will provide.
Labels: blacksmithing, iron smelting, museums - teaching